Gunite Hose Selection: Part 2
Updated: May 2, 2023
In the previous article we discussed the choice of gunite hoses based on strength or flexibility and gave reasons and examples of reasons a gunite contractor would choose the strongest or most flexible gunite hoses. We also began to explore hose specifications. In this edition, we'll focus on how these specs play into the gunite contractor's choice of a gunite hose. Again the most common specs or technical data on gunite hoses include tube (interior) and cover (exterior), info about a reinforcement layer in the hose, temperature range, inside diameter, weight and working pressure.
The gunite hose tube or interior of the hose is essentially THE hose. Gunite material, dry sand and cement, travels though this part of the hose and it is designed to handle these dry abrasive materials in the most efficient way possible. This interior of the hose is commonly a gum rubber material which has been proven in the field by gunite contractors and gunite pool building to be the best suited type of rubber to use for the hose makeup. It is important to note that any gunite hose will wear out over time once enough abrasive materials have eroded the gunite hose. It is the responsibility of the gunite crew to inspect gunite hoses for wear and replace them as needed. On the outside of the hose tube, the gunite hose is wrapped with a synthetic rubber cover for protection, safety and added strength. Between these two layers, of the hose, the manufacturer adds a synthetic or polyester fabric layer, which allows the manufacturer to control the strength and flexibility of the overall gunite hose. More layers of fabric equals a stronger, longer lasting gunite hose. Less layers of fabric equate to a more flexible gunite hose that may have some sacrifice in strength or service life, depending on the application, materials and experience of the gunite contractor. These factors always come into play in any discussion of service life btw.
The next specification to explore is temperature range, Arguably the most useless piece of data, the coldest or hottest that a hose can get is very rarely any consideration of the gunite contractor. Concrete work in general cannot take place at extreme low temps but if you were to find a way to apply gunite below freezing, the gunite hose would hold up fine with low temps down to about -30 F. On the high temperature end, there is neither a concern since any heat involved in gunite construction should not put the gunite hose in any risk of exceeding high temperatures. But the highest temp that gunite hoses will operate is around 175 F.

Hose diameter is a more useful specification. These days the gunite industry has more or less simplified the hose diameters to two choices, 2 inch and 1-1/2 inch., both referring to the inside diameter or ID. The easiest way to understand why gunite contractors would choose one diameter over the other comes down do the application, that is, what are they doing? Is it new construction or is it repair of an existing structure. Nine times out of ten, gunite contractors working on new construction will use 2 inch diameter gunite hoses. These larger diameter allows the most production, output, and coverage for gunite construction jobs like pool construction, new retaining walls, soil stabilization, tunnels, and even innovative projects like concrete homes and skateboard parks. When the project calls for concrete repair work using the gunite process, the contractor will typically select a 1-1/2" diameter hose. The diameter hose is compatible with the amount of production needed to resurface concrete using the gunite repair process. These projects include concrete column repairs, concrete bridge repairs, concrete embankment repairs and a very popular use of the 1-1/2" hose - furnace relining, to name just a few example concrete repair projects using gunite hoses.
Next specification, the weight of the hose is fairly standard across the gunite industry, regardless of manufacturer. So, gunite contractors aren't really picking their hoses by looking at these weights, typically in lbs/ft. But, this data can be useful in determining shipping weights/rates or for verifying weight of alot of gunite hoses being hauled on a trailer to meet DOT specs, for example.
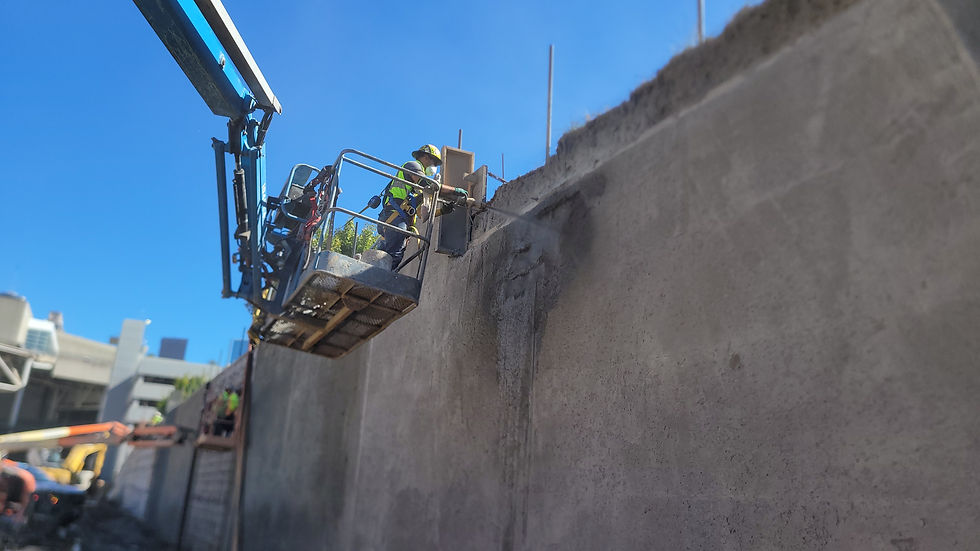
Lastly, working pressure is an important spec of the gunite hose for the sake of safety. The pressure at which a gunite hose can safely be used must be considered by the gunite contractor to keep the crew safe from hose "blowouts" which are the protrusion, cuts, unbraiding, puncture or otherwise failure of the hoses during operation. Typical gunite hoses are able to withstand approx 150 psi of pressure, which is controlled normally by the gunite machine operator on the job. This member of the gunite crew is usually responsible for controlling the air compressor and the gunite machine, which both have valves and gauges to control and monitor pressures throughout the system, which conveys (blows) sand and cement, gunite materials, into the gunite hoses. It is a critical safety measure to keep these pressures below the operating pressures of the gunite hoses to help avoid any issues. Gunite contractors must always select gunite hoses that will provide the operating pressures that will come into play using their particular gunite equipment.
Fortunately these gunite hose specifications are not alot of information to keep track of and when it comes down to it, gunite contractors should be able to select the right gunite hose for their job fairly quickly. By considering gunite hose specifications and partnering with a professional supplier like Gunite Shotcete Warehouse (GSW) who is readily available to help review these specifications, the gunite contractor can get to back work doing what they do best!
Comments